In the world of modern technology and rising quality standards, the process of bending copper tubes is continuously evolving. For many companies, traditional bending methods are not precise enough, leading to material losses and additional associated costs. In response to these challenges, more and more enterprises are opting for CNC tube bending – a precise, efficient, and fully repeatable method. But why is this happening, and what are the real benefits of this decision?
Don’t Overdo It!
When traditional methods give way to CNC bending services
CNC tube bending has become a key process in the refrigeration industry, especially in the context of copper pipes. Thanks to their excellent anti-diffusion properties and corrosion resistance, copper tubes are widely used in refrigeration systems to connect components. They play a crucial role in monoblocks, condensing units, and other advanced refrigeration systems.
Among the undeniable advantages of CNC tube bending, its versatility is also worth emphasizing. This technology allows not only precise bending in 2D, but also advanced 3D bending, opening up possibilities for the production of complex details. CNC benders are not limited to processing copper tubes. They easily handle bending pipes made of other materials such as steel, stainless steel, and aluminum. Thanks to their advanced functions and appropriate equipment. CNC bending technology and pipes of various materials find wide application. For example in the automotive, aviation, medical, and construction sectors, where the accuracy and repeatability of tube shapes play a key role.
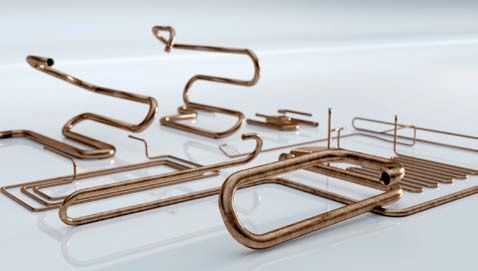
Advantages of CNC bending
- Time and money savings – machine bending is much more efficient than manual bending. This translates into measurable financial and time savings, especially for larger production batches.
- Elimination of waste and shortages – ordering pre-made components according to project specifications reduces waste generated in the production process. This is beneficial from both an economic and environmental point of view.
- Just In Time – traditional tube bending methods involve storing a large amount of material and coordinating production. Thanks to outsourcing CNC bending, companies do not have to worry about logistical aspects and can carry out projects according to schedule.
- Ease of ordering – modern CNC bending technologies do not require clients to provide precise technical documentation. In many cases, a single photo and basic dimensions of the detail are enough. This not only speeds up the ordering process, but also facilitates communication and reduces the risk of errors.
- Endforming – an additional advantage is the ability to perform specialized end forming of pipes (expansion, flaring, etc.). This offers a wider range of applications and allows customization of the detail to specific project requirements.
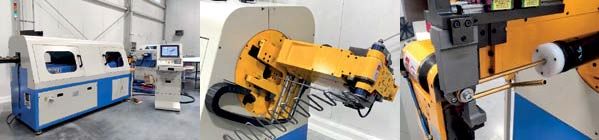
Are you interested in CNC tube bending services?
We encourage you to learn more about the offer and contact the technical department of AiFO Components.