When thinking about a refrigeration unit, do we consider the condensing unit and its components? It’s not unusual, as its primary task is to remove heat from the inside of the device. However, this is only possible through the proper cooperation and alignment of all other system elements. One of of the key components in most refrigeration devices is the magnetic gasket that seals the door connection to the body of the furniture. At this point, one might ask, “But how is a gasket the key equipment of a gasket the key equipment of a refrigeration unit? Isn’t the cooling system the heart of this device?”Yes, the cooling system is the heart, but the organism needs other vital organs to function properly!
Let’s go back to January 28, 1986, at 16:39 UTC. The Challenger shuttle disaster occurs, disintegrating due to damage to the O-ring seal in the right solid rocket booster engine. It was the seal damage that led, 45 seconds into the flight, to an increasing stream of fire, causing the tank’s lining to burn out, the shuttle assembly to disintegrate, and to be crushed by aerodynamic forces.
The mission designated STS-51-L, in which the space shuttle Challenger disaster occurred, ended in a tragic event that highlighted how even minor and seemingly trivial elements can be crucial. A large space shuttle, powerful engines, and large fuel tanks, but the disaster occurs due to a small component – a seal. Comparing a space shuttle to a refrigeration device may seem a bit exaggerated, but it illustrates the point and shows how important a seal is in a device, and reminds us that it needs proper care.
DEFINITION OF A SEAL
“Everyone knows what a horse is” – a quote from the encyclopedia of Benedykt Chmielowski known to almost everyone. A similar statement could be used to define a seal. After all, a seal is a simple element – a type of sealant – with a specific shape and dimensions. It is placed in the profile of refrigeration doors, at the connection point with the body of the cooling furniture, allowing for proper sealing. Thanks to gaskets, both static and dynamic seals can be performed.
Tasks and role of gaskets
Gaskets are an integral part of many devices that we all use every day. Their main tasks and roles include:
- isolation from the environment,
- maintaining liquid pressure,
- maintaining gas pressure.

AiFO Components are specialists in the refrigeration industry. The company’s employees are eager to share their valuable, long-term experience by educating on the production, selection, and handling of various components, including magnetic seals.
Properly selected and installed welded magnetic gasket ensures the tightness of the cooled chamber in the refrigeration furniture at an ideal level. This translates into efficient operation of the cooling system and temperature stability in the chamber, leading to financial savings. On the other hand, a poor-quality or damaged seal that is not sufficiently tight will cause icing of the evaporator, water condensation on the body, problems with maintaining proper hygiene levels, leading to increased work and extended operation time of the cooling system. This, in turn, increases the cost of operating the device, resulting from higher energy consumption.
The wide spectrum of applications of seals in various industries only shows how important they are in many systems, devices, and places.
Improper storage, faulty installation, and poor protection during transport – these events can lead to seal damage, which can cause undesirable situations. Insufficient isolation from the environment, leakage, contamination are cases everyone wants to avoid. These can be averted by handling seals properly, not exposing them to changes in properties.
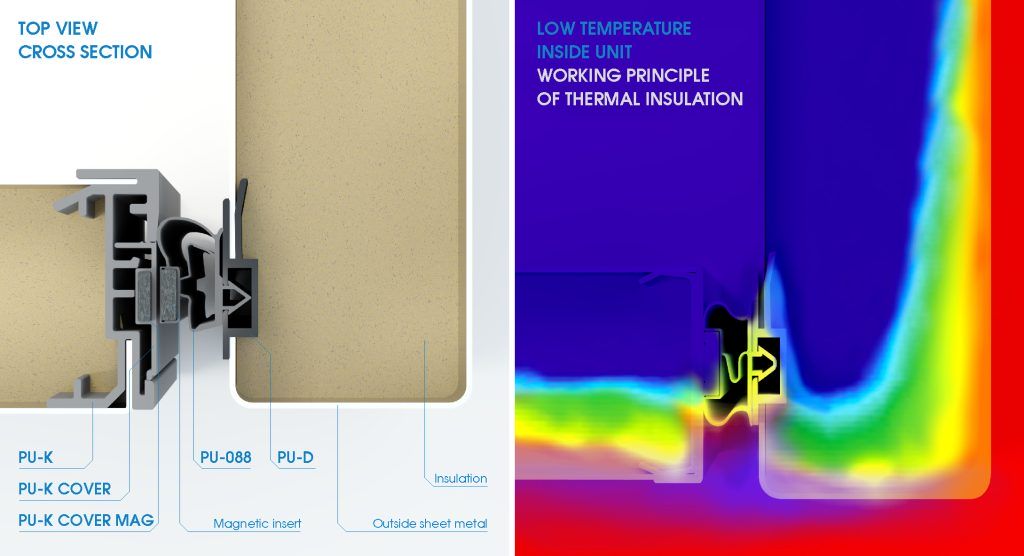
What to pay attention to?
Important parameters in the production of magnetic seals are the material and quality of the seal. Gaskets produced at AiFO Components are made in the process of extrusion of soft PVC plastics. In addition to PVC (polyvinyl chloride), TPE (thermoplastic polyester elastomer) is also used in the production of seals. The offer includes multi-chamber seals, which, depending on the installation method, are pressed, glued, or screwed into the profile.
How is the production process?
After extrusion in the extrusion process, the seal is cut to the appropriate size. Then a magnet is inserted into the appropriate pocket of the gasket – standard polarization is S N S. AiFO Components has magnetic inserts with an attraction force from 31 to 75 g/cm². The next stage is the welding of the gaskets, a process carried out on automatic welding machines. This allows for achieving a tight, even, and durable weld and high repeatability. Each stage of seal production ends with quality control of the product. Control during the process, as well as final quality control, eliminates all potential irregularities, guaranteeing the highest quality products.
Construction elements of the gasket, which determine the tightness between the doors and the body of the refrigeration, low-temperature, or ultra-low-temperature device, include:
- Multi-chamber profile – provides better thermal insulation and increases the tightness of adhesion to the body;
- Shock absorber – responsible for contact during the closing of doors or drawers with the body and tightly adhering to the body profile;
- Quality of the weld – a properly made welded connection should be smooth and ensure the tightness of the gasket in the corner;
- Magnet – the built-in magnet attracts the seal to the magnetic element installed in the profile of the cooling furniture body.
REMEMBER!
- Proper storage of gaskets will protect them from deformation and dimensional changes, while ensuring their excellent usability. Seals should be stored in dry and properly ventilated rooms, avoiding situations where the packaging may deform due to excessive humidity or improper storage.
- The ideal storage temperature for gaskets ranges from 5 to 35°C, and the humidity should be around 60%. Lower temperatures can lead to increased seal stiffness, while higher temperatures can lead to dimensional changes. The proper temperature of the seal before installation should be from 20 to 25°C. Gaskets must be kept in their original packaging in which they were delivered. It is permissible to store seals outside the original packaging, on specially designed stands, where the top and bottom of the seal will be supported.
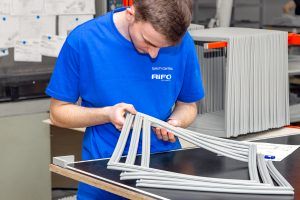
During the inspection and maintenance of the refrigeration device, one should not focus solely on works related to the cooling system or electrical system. Attention should also be paid to the technical condition and level of wear of the seal.
Another important process related to the production of seals is their packaging and storage method. They require special attention and due diligence to ensure their shape, dimensions, and properties do not change. Years of experience in welding magnetic seals have allowed AiFO Components to refine and standardize the process of packaging and storing gaskets.
AiFO Components has been manufacturing magnetic gaskets for the refrigeration industry since 2013. This certainly entitles us to believe that our employees have sufficient knowledge and experience to share with our customers. In our offer, in addition to seals and PVC profiles, you can also find other components used in the production of refrigeration, low-temperature, and ultra-low-temperature devices, such as: condensers, evaporators, heaters, fans, and other components. – We perfectly understand how all these elements of the cooling system work together! – emphasize the representatives of AiFO Components.
Take care of the gaskets!
During the inspection and maintenance of the refrigeration device, one should not focus solely on works related to the cooling system or electrical system. Attention should also be paid to the technical condition and level of wear of the seal. If the cooling furniture is unable to achieve its original performance, even though the surrounding conditions have not changed. It could be signs suggesting problems with the cooling system, iced evaporator, or contaminated condenser, but also – with a faulty seal. In this case, an appropriate inspection should be carried out to find the faulty component in the device. Signs that may indicate wear or damage to the seal include:
- no breaks in the compressor’s operation,
- presence of condensate inside the device’s chamber,
- iced evaporator,
- spoiling food products.
The above symptoms, of course, do not necessarily mean that it is definitely the fault of the seal. They can be more serious problems related to, for example, a refrigerant leak, contaminated condenser, or iced evaporator, as well as a poorly leveled device, or loose hinges in the refrigeration doors. Regular maintenance of the device helps avoid unwanted events and timely respond to irregularities. Timely reaction allows avoiding increased electricity consumption costs and device operation disturbances, and any repair or replacement of a given component will be cheaper than the entire system. It is therefore worth taking care of your refrigeration devices, including seals, to avoid disaster!